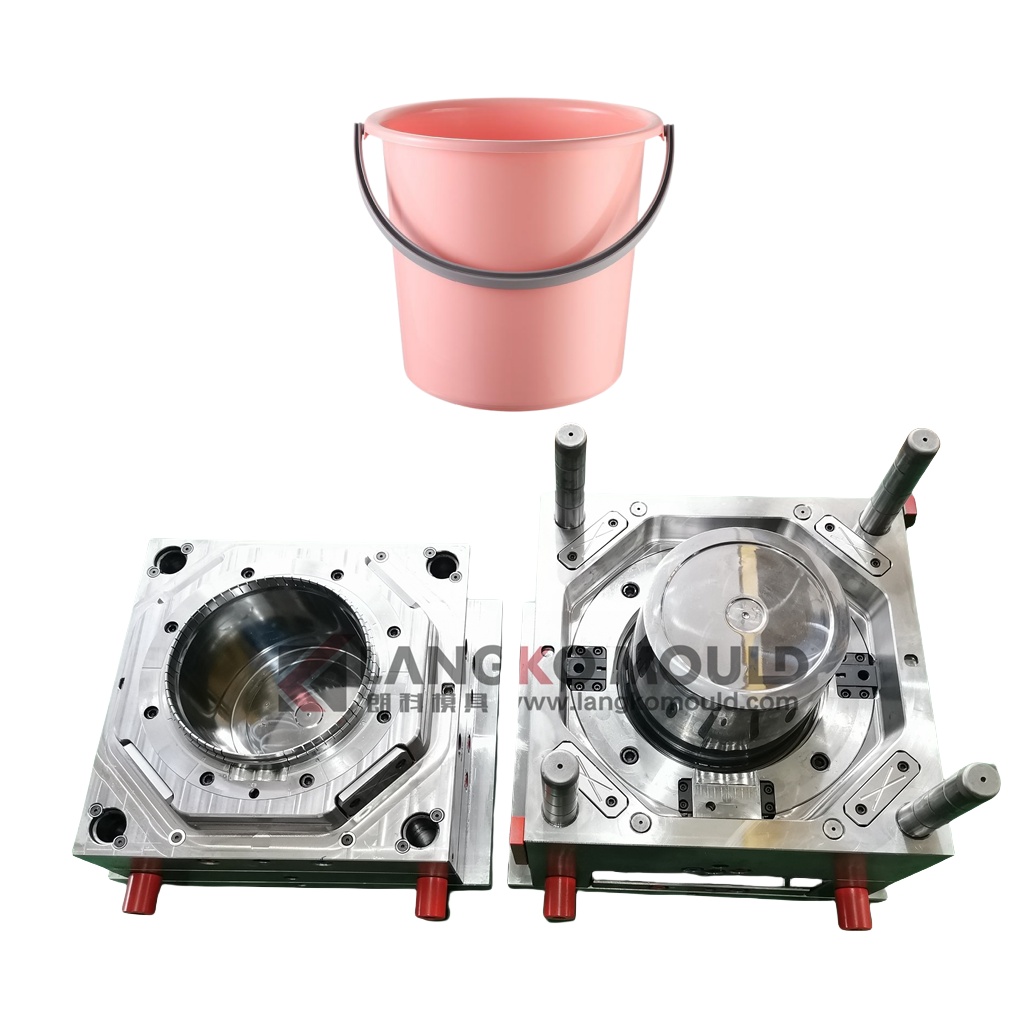
Plastic bucket injection mold is an indispensable tool in modern manufacturing. It uses high temperature and high pressure to melt plastic and inject it into the mold cavity. After cooling and solidification, it forms a plastic bucket of the desired shape. This mold design and manufacturing technology is widely used, especially in the packaging, chemical, food and other industries. Plastic bucket are widely used because of their lightness, low cost, and easy large-scale production. For example, for a standard 50-liter plastic bucket, its injection mold design must take into account the fluidity of the material, the cooling rate, and the strength and durability of the finished product. During the design process, mold engineers will use computer-aided design (CAD) software for precise modeling to ensure that every detail meets production requirements. In addition, the innovation of mold design is also crucial. It not only affects the quality and production efficiency of plastic bucket, but is also directly related to the market competitiveness of enterprises.
The importance of plastic bucket injection molds is reflected in their profound impact on modern manufacturing. As the core tool for the production of plastic products, the design and manufacturing of injection molds are directly related to the quality and production efficiency of the products. Taking plastic buckets as an example, this kind of container is widely used in food, chemical, pharmaceutical and other industries, and its production efficiency and quality directly affect the market competitiveness of enterprises. According to relevant statistics, the precision and stability of injection molds can improve production efficiency by up to 30%, while reducing the scrap rate, thereby significantly reducing production costs. When designing plastic bucket injection molds, factors such as material fluidity, cooling rate and shrinkage must be taken into account to ensure the dimensional accuracy and surface quality of the final product. For example, the use of high-fluidity plastic materials can reduce injection pressure, reduce mold wear and extend the service life of the mold. In addition, innovations in mold design, such as the introduction of intelligent technology, can achieve automated production and further improve production efficiency and product quality.
In the full analysis of the design and manufacturing of plastic bucket injection molds, the basic principles and processes of mold design are the key to ensuring the quality of the final product and production efficiency. First of all, the preparatory work before design includes a detailed analysis of the size, shape, function and production volume of the plastic bucket. This step is crucial because it is directly related to the rationality and feasibility of the mold design. For example, according to the volume and intended use of the plastic bucket, the size and structure of the mold can be determined, which affects the selection of materials and the subsequent injection molding process.
In terms of the basic principles of mold design, the principles of "minimizing material waste" and "maximizing production efficiency" must be followed. For example, by using computer-aided design (CAD) software, designers can accurately calculate the flow path and cooling time of plastic materials, thereby optimizing the design of the gate system, reducing material waste and shortening the production cycle. In addition, the maintainability of the mold and the convenience of troubleshooting should also be considered in the design process to ensure the stability and reliability of the mold in long-term use.
In the design process, from conceptual design to detailed design, and then to the final mold manufacturing and testing, each step must strictly follow the established process. For example, the parting surface design of the mold requires precise calculation to ensure the appearance and structural integrity of the plastic bucket, while also considering the convenience of disassembly and assembly of the mold. In the mold manufacturing process, the processing technology of the mold parts must be precise to ensure the accuracy and durability of the mold. By adopting high-precision CNC machine tools and advanced processing technology, the dimensional accuracy and surface finish of the mold parts can be ensured, thereby improving the production quality of the plastic bucket.
In summary, the full analysis of the design and manufacturing of plastic bucket injection molds not only needs to follow the basic principles and processes, but also needs to combine modern technologies such as CAD and CAM (computer-aided manufacturing), as well as a deep understanding of material properties, in order to design both economical and efficient molds to meet the needs of modern industrial production.
Sale Engineer: Luna He
E-mail: market@langkomould.com
Wechat / WhatsApp/ Tel: +86 13306762335
Facebook: https://www.facebook.com/langkomould
Website: https://www.langkomould.com/
TAIZHOU HUANGYAN LANGKO MOULD CO.,LTD
ADD: NO.345, XINJIANG ROAD, XINQIAN STREET, HUANGYAN, 318020, TAIZHOU, ZHEJIANG, CHINA