With the vigorous promotion of new energy vehicles, the demand for plastic battery box mold is also increasing. Plastic battery box molds not only has high quality and ensure products not deform,but also dose not leakage after the cover is closed.This is high demand of plastic battery box mold design.
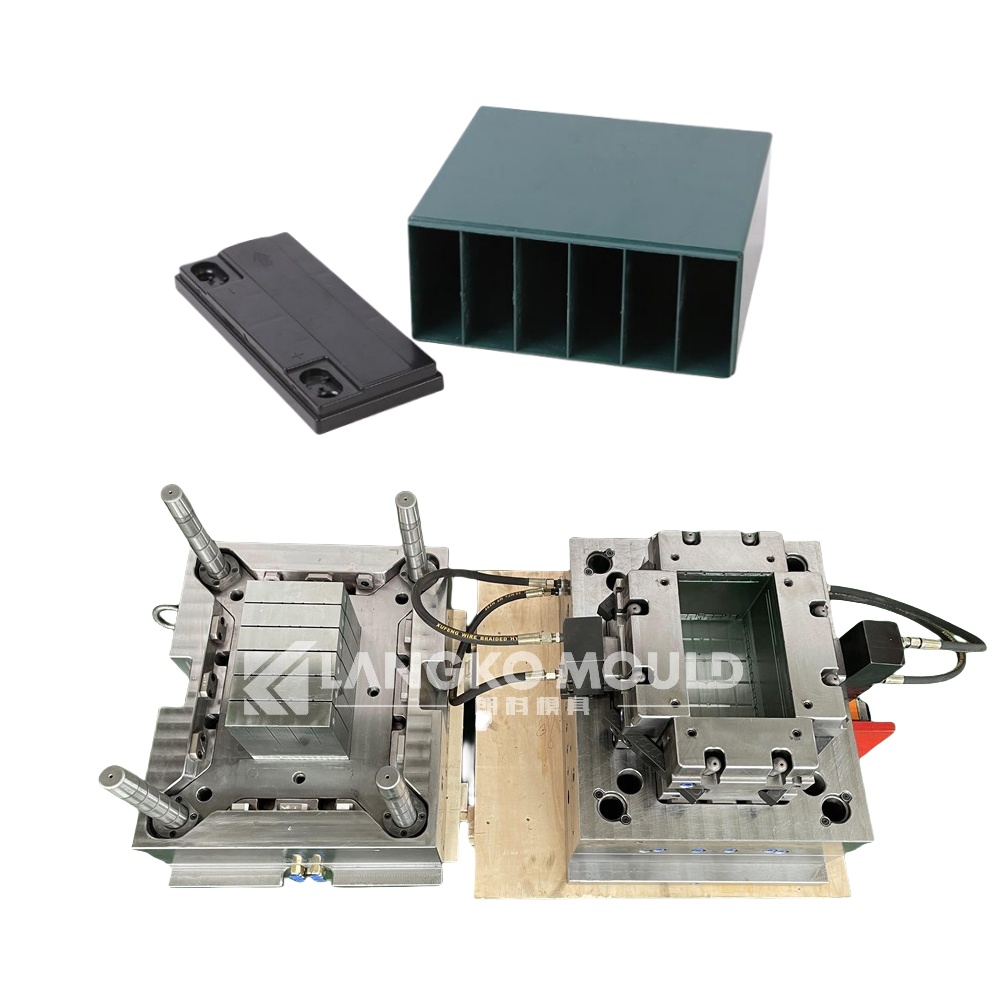
There are 3 main points:
1. The product's ability to resist deformation,calculate shrinkage size based on material shrinkage,controlling the size of the deformation,make the product look linear.In addition, the demoulding slope of the battery box mold should be as small as possible, with a slope of 0.5 degrees.
2. Plastic battery box mold usually has 6 inner boxes,so we need 1 inner box with 1 tip hot runner,to ensure 6 inner boxes molding in the same time of the product injection molding.
3.The third tip is cooling line,by reason of 6 inner boxes size are not large,so the cooling holes need designed to be thin and long.To ensure uniform cooling effect of 6 inner boxes.The processing of cooling line holes can be carried out smoothly.
Plastic battery box mold cooling system
To make a good plastic battery box mold, need to simulate the injection molding process of the battery box, do mold flow analysis, In accordance with set the injection pressure, time, speed of injection mold. Analyze the problems that the battery shell mold will encounter in the production process, such as the location of air trapping the location of the weld, and their relative position for high-pressure injection, find the problem points, avoid these problems in the actual production process, and reduce losses.
Plastic battery box mold used multi-tip hot runner injection, one battery cell usually with one tip hot runner, to ensure injection pressure, time speed in same time of every battery cell, to avoid deformation of the battery boxes. If the product cost budget is sufficient, we suggest to use multi-tip valve pin gate hot runner. the battery box will be more beautiful.
It is ejector plate to ejector of ejection structure. In view of draft angle of battery box is small, The product will be difficult to ejection, need ejector plate help product ejection. Then cooperate with the robot to pick up the product.
Compared with other injection molds, the cooling system of the battery box mold is more complicated. You cannot simply design a straight water path, but a multi-tube curved loop. Every part of the product needs to have a water path. Especially the liner, the 6 core positions and water paths should be numerous and detailed. Please ensure that the mold can be cooled in time during the injection process.
The processing of plastic battery box mold is similar to that of tray mold. It is divided into many small inserts and processed separately, which can save processing time and reduce error costs.
The injection molding of battery box mold can be tested by querying mold flow analysis data. Set the appropriate pressure, injection time and injection speed to see if the injection molded battery box can achieve the expected effect.
As a plastic battery box mold manufacturer with mature technology, Longko Mould will always be your first choice.
Sale Engineer: Luna
E-mail: market@langkomould.com
Wechat / WhatsApp/ Tel: +86-13306762335
Facebook: https://www.facebook.com/langkomould
Website: https://www.langkomould.com/
TAIZHOU HUANGYAN LANGKO MOULD CO.,LTD
ADD: NO.345, XINJIANG ROAD, XINQIAN STREET, HUANGYAN, 318020, TAIZHOU, ZHEJIANG, CHINA