With the widespread application of plastic products in daily life and industrial production, injection preform molds, as key tools for plastic bottle production, are becoming increasingly important. This guide aims to provide comprehensive guidance for technicians engaged in the design, manufacture and use of preform injection molds, covering all aspects from mold design to maintenance to ensure the production of high-quality preform products.
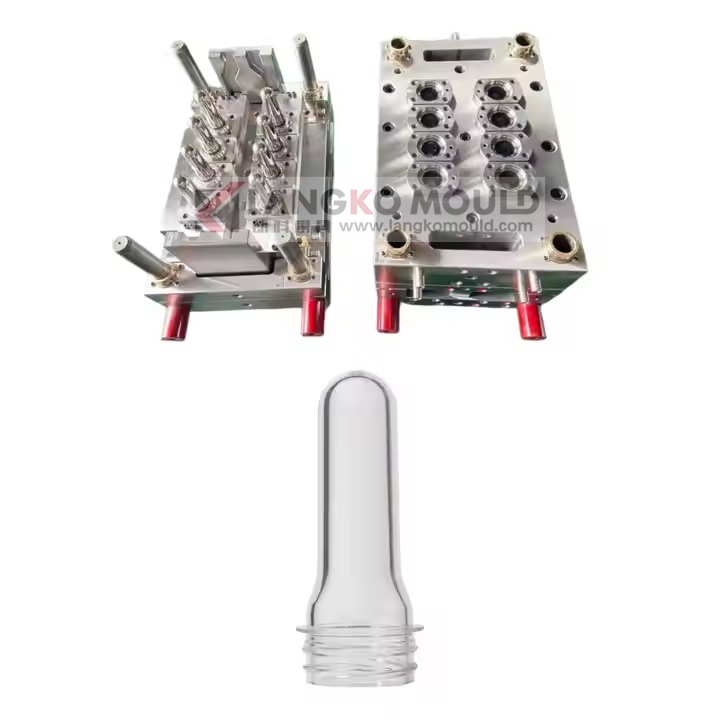
1. Mold design
Mold design is the first step in the manufacture of preform injection molds, and its quality directly affects the performance and appearance of the final product. The following are the key steps and precautions for mold design:
Product Analysis:
Material Selection: Choose the appropriate plastic material, such as PET, PP, HDPE, etc., according to the purpose of the preform. Different materials have different physical and chemical properties. Choosing the right material can ensure the strength, transparency and chemical resistance of the preform.
Size and Shape: Determine the size, wall thickness and shape of the preform to ensure that it meets the product design requirements. The size and shape of the preform not only affects its appearance, but also its fluidity and cooling effect during the injection molding process.
2.Mold structure design:
Cavity and core: Design reasonable cavity and core structure to ensure the molding accuracy and surface quality of the preform. The design of the cavity and core should take into account the shrinkage rate and cooling time of the material to avoid deformation and defects.
Runner and gate: Optimize the design of runner and gate to ensure that the plastic melt fills the cavity evenly and reduces injection defects. The design of the runner should minimize pressure loss, while the position and size of the gate should ensure that the melt can evenly fill the entire cavity.
Cooling system: Design an efficient cooling system to shorten the molding cycle and improve production efficiency. The design of the cooling system should consider the layout and diameter of the cooling channel to ensure that the preform can be evenly cooled and reduce internal stress and deformation.
Mold material selection:
Steel selection: Select appropriate mold steel according to production requirements, such as P20, 718, S136, etc., to ensure the durability and precision of the mold. Different steels have different hardness, wear resistance and corrosion resistance. Selecting the right steel can extend the service life of the mold.
Surface treatment: Perform appropriate surface treatment, such as nitriding, chrome plating, etc., to improve the wear resistance and corrosion resistance of the mold. Surface treatment can improve the surface hardness and finish of the mold, reduce wear and corrosion, and extend the service life of the mold.
Sale Engineer: Luna
E-mail: market@langkomould.com
Wechat / WhatsApp/ Tel: +86 13306762335
Facebook: https://www.facebook.com/langkomould
Website: https://www.langkomould.com/
TAIZHOU HUANGYAN LANGKO MOULD CO.,LTD
ADD: NO.345, XINJIANG ROAD, XINQIAN STREET, HUANGYAN, 318020, TAIZHOU, ZHEJIANG, CHINA